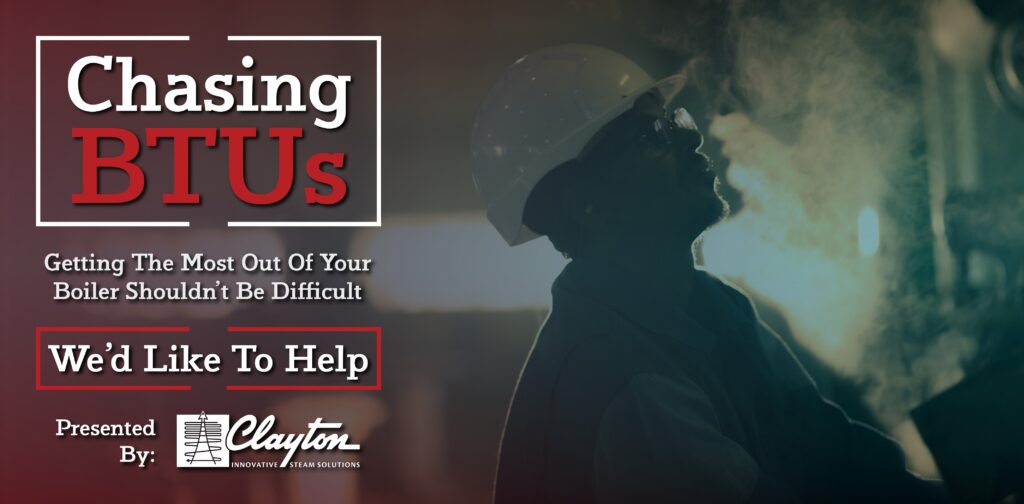
Getting The Most Out Of Your Boiler System
Understanding your boiler system shouldn’t be difficult. Despite this, there’s an unfortunate trend in the industry toward over complication, cluttered with confusing terminology and explanations. Finding good information can be especially frustrating, as educational sources can quickly turn into a disguised sales pitch—written with a heavy bias toward the author’s company or product line.
Whether you’re a first-time buyer, considering a replacement, or just looking for ways to improve your existing steam system, this article is for you. In it, we’ll share practical advise to help you get the most out of your steam system, regardless of your supplier or situation.
Efficiency Saves You Money
Efficiency has the greatest impact on your annual costs. In any boiler application, you want your steam system to be running as efficiently as possible. The better your efficiency, the less fuel your boiler burns, and the less you spend. Fuel prices are continuing to rise, and the annual cost to operate a boiler can be up to three times that of a new boiler installation. When it comes to comparing similar manufacturers, be sure to prioritize efficiency ratings, as even a small increase has the potential to offset installation costs in the first year alone.
Size Matters
Most boilers operate at a peak efficiency during high firing rates. If your boiler is oversized, it operates at lower firing rates, driving down efficiency and raising costs. Conversely, an undersized boiler will struggle to meet demands, causing delays while your production falls behind. In both of these cases, a potential supplier should provide a personalized solution, tailored to the needs of your facility, and account for the possibility of future expansion.
Maintaining Combustion Rates
In order to keep your boiler firing at an ideal rate, your burner requires excess air. However, this excess air needs to be calculated and calibrated to a specific amount, as too much, or too, little results in wasted energy. Instead, you end up with unburned fuel, carbon monoxide, or soot, all of which reduce heat transfer. This means your boiler is now burning extra fuel just to reach previous results.
Combustion control systems are a great way to keep a close eye on these rates. These programs can keep an eye on your air-to-fuel rates and make automatic adjustments based on the changing conditions in your plant. This can also be paired with oxygen sensors in your exhaust stack for even better performance.
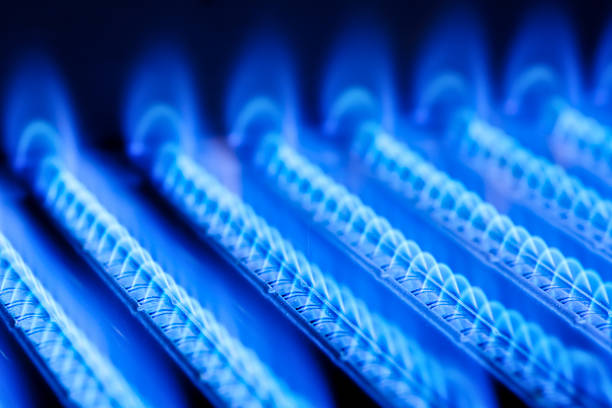
Essential To Guarantee Proper Heat Transfer
Water Treatment
All boilers require water treatment, and keeping up with a plan is crucial. All water contains impurities in the form of dissolved solids or excess gases, which water picks up and carries based on its natural environment. As your boiler converts water into usable steam, these impurities remain and accumulate in your boiler.
If left unchecked, this can wreak havoc on your boiler’s internal systems. Internal parts can become corroded and cause leaks, or leftover impurities can begin to build up inside the boiler. These leftovers restrict the flow of steam and water, as well as lowering your boiler’s heat transfer, and possibly result in a shutdown. A buildup as little as 1/8″ can reduce efficiency by as much as 3%. Proper water treatment removes as us much of these impurities as possible, protecting your steam system.
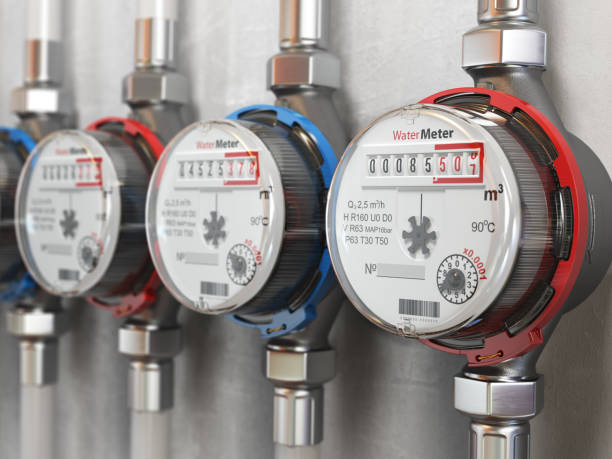
Monitor TDS Levels
TDS, of Total Dissolved Solids, are the residual impurities discussed above. Since its impossible to remove all of these impurities completely, each boiler has a total TDS level that it can operate under without a dip in performance. To control TDS levels, boilers make use of a procedure called blowdown, a periodic removal of water from the system that flushes out these undesirables.
While necessary, blowdown can be costly. The water being dumped has been paid for three times over, in the forming its delivering, its treatment, and its heating. With this in mind, a boiler that is capable of operating under higher TDS levels also requires less blowdown and less wasted water.
The Economizer Section
An economizer is a great way to improve boiler’s efficiency. Most boilers produce exhaust gases, which are typically vented. An economizer makes use of these otherwise wasted gases by using them to as a heat source, which may preheat your boiler’s feedwater or be an extension of the boiler itself, depending on the design. Though it adds an upfront cost, an economizer quickly pays for itself by lowering fuel costs.
Bring Back The Condensate
As stream travels through piping, some of that steam will inevitably condense, and return to water. Many installations consider this water to be useless and simply dump it down the drain alongside their blowdown – a huge waste of energy and money. Similar to blowdown, this water has been delivered, heated, and treated. Capturing condensate and returning it to your feedwater tanks saves on delivery, heat, and treatment. Since this water is near boiling temperature and realitivly pure, it reduces your boiler’s workload and once again improves efficiency.
Regular Maintenance
Another bad habit in the boiler industry is neglecting regular maintenance, a practise that can allow your boiler’s performance to drop significantly over time. Most suppliers will recommend a maintenance schedule to you along with a new purchase to ensure reliable operation.
While there can be temptation to delay maintenance and save money, you’ve already made a significant investment in your steam system, and protecting that investment is important. While calling a technician regularly may seem unnecessary, the alternative can be a plant wide shutdown, or an expensive repair. Regular service helps to identify any potential problems early and keep operations running smoothly.
Insulation
While adequate insulation is typically standard on newer systems, it’s still worthwhile to take a closer look at the boiler itself and throughout your steam system. If your boiler is warm to the touch, or worse, dangerously hot to the touch, you’re not just paying to heat water, you’re paying to heat the entire room. Be sure to compare insulation between potential suppliers, as a well insulated boiler will lower fuel use by directing that heat back where it belongs.
The same is true of the pipes in your plant. Any hot surface should be insulated in order to keep the heat inside, instead of radiating into the air. Without insulation, your steam will condense prematurely, and your boiler will have to work even harder to fulfill steam demands. Modern installations should include this, but if you find yourself managing an older system, consider inspecting your steam lines for areas where insulation is removed, damaged, or missing.
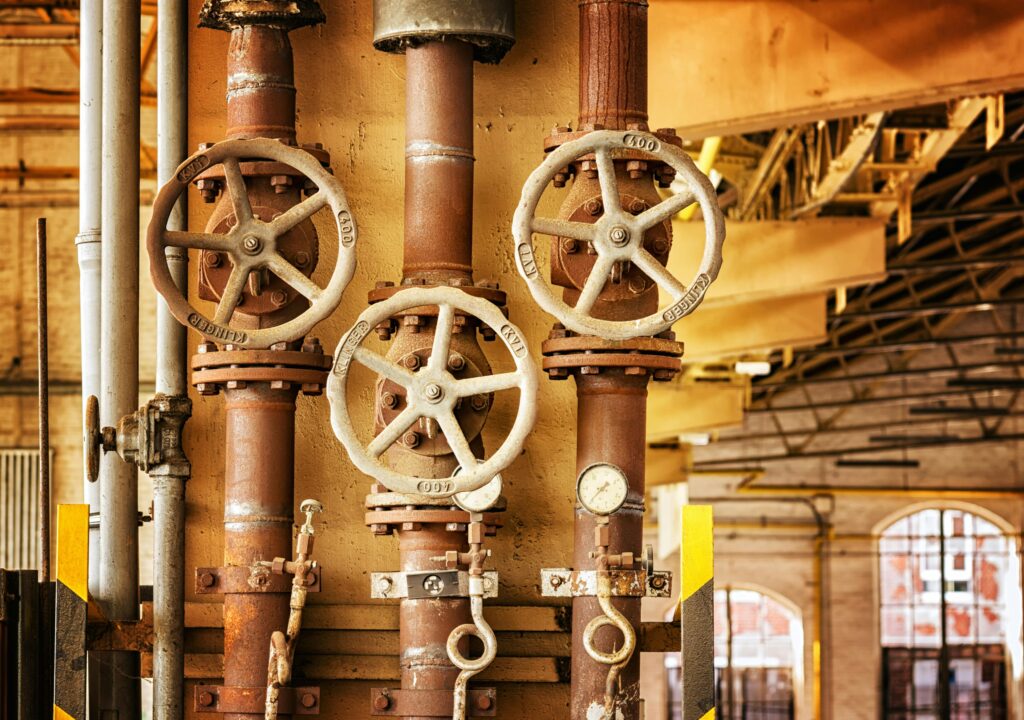
Regardless of your current situation, we hope that these tips will help you to get the most out of your existing steam system, or provide some helpful insight when considering a new purchase.