When it comes to keeping things running smoothly in the beverage industry, reliable steam generation is crucial. Whether it’s producing thousands of gallons of wine daily or crafting small- batch spirits, the right equipment makes a big difference. As showcased in two articles in Project Report, for Bronco Wine Co. and CH Distillery, Clayton steam generators have been key players in their operations.
The Beverage Demand
Bronco Wine Co., located in Ceres, California, is one of the world’s largest wineries, producing nearly 186,000 gallons of wine daily. The company’s significant scale demands a dependable and efficient steam supply for various processes, including heating, sterilization, and cleaning. The San Joaquin Valley, where Bronco is based, is known for its stringent air quality regulations, requiring the use of low NOx (Nitrogen Oxide) burners to minimize emissions.
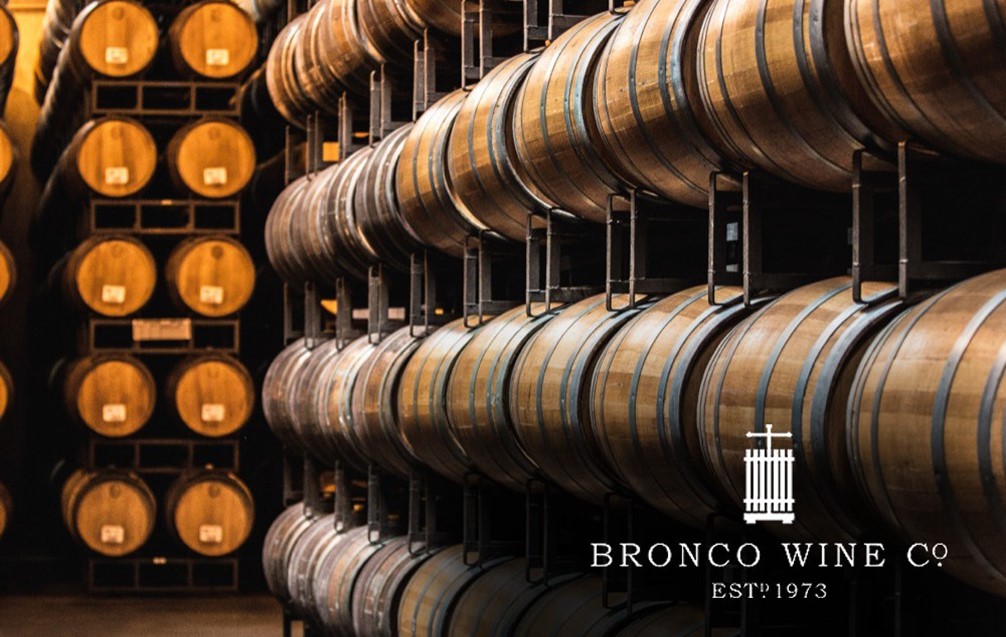
CH Distillery, a newer entrant in the beverage industry, operates out of Chicago. The distillery, which specializes in vodka, gin, rum, and other spirits, depends heavily on steam for its production processes. Unlike traditional vodka production methods that use industrial ethanol, CH Distillery’s approach involves creating vodka from scratch, which requires substantial heat for mashing, fermenting, and distilling grains. The distillery’s urban location also demands equipment with a compact footprint and high safety standards.
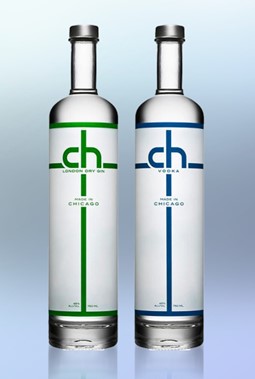
The Clayton Solution
When Bronco Wine Co. and CH Distillery were faced with the need for reliable steam generation, both turned to Clayton Industries. Each company evaluated their specific requirements and found that Clayton’s steam generators were well-suited to their needs.
For Bronco Wine Co., the decision was driven by Clayton’s fast startup times, compact size, and low NOx burner technology. As reported by Sarah Annese in Project Report, Paul Franzia, Director of Engineering and Environmental Affairs, highlighted the importance of the generators’ quick load response and high efficiency in maintaining production without significant energy loss. The generators’ small footprint allowed for flexibility in placement across various locations, and their low blowdown rate minimized water waste. The steam generators have been operational for over eight years, consistently meeting the company’s needs for heating, sterilization, and cleaning.
CH Distillery selected Clayton steam generators for their compact design, reliability, and safety features. Similarly outlined in Project Report, the distillery initially installed a 75-horsepower generator, which provided necessary heat for the entire distillation process. Impressed by the performance, CH Distillery expanded by installing two 200-horsepower generators in their new facility. Tremaine Atkinson, co-founder of CH Distillery, emphasized that the generators are critical to their production process, describing them as the “fuel” for their operations.
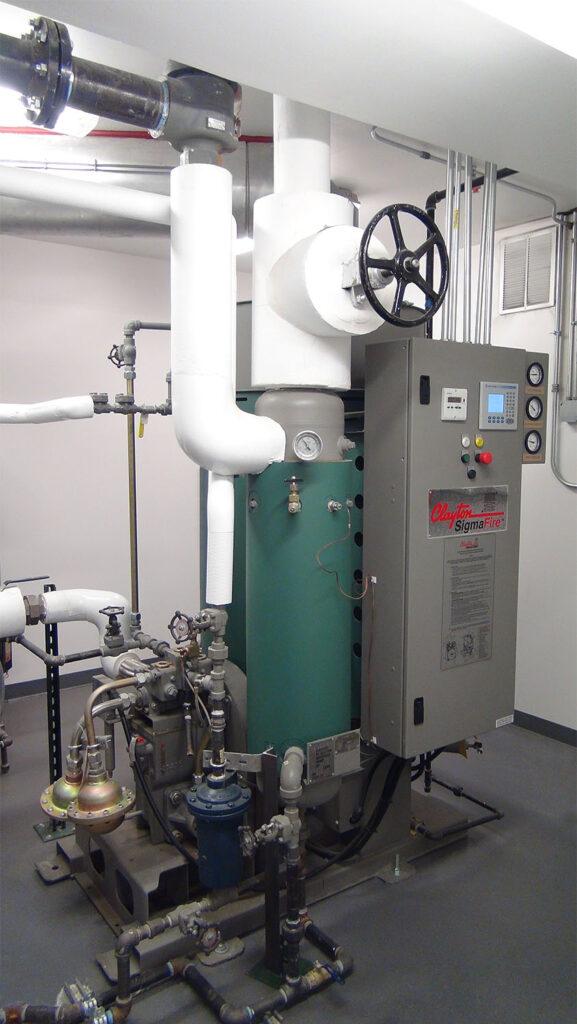
Steam Technology Driving Production Success
For Bronco Wine Co., the Clayton steam generators have contributed to significant operational efficiencies. The generators’ rapid startup capability and minimal maintenance requirements have streamlined production and reduced energy consumption. This efficiency has also supported compliance with local air quality regulations and facilitated the company’s expansion plans.
CH Distillery has experienced substantial growth since implementing Clayton steam generators. The reliable and efficient heat provided by the generators has been integral to scaling up production from 15,000 cases to a projected 150,000 cases. The success of these generators has encouraged further investment in Clayton equipment for their new facility, supporting both increased production capacity and the introduction of new product lines.